Impact Resistant: Polycarbonate material was originally made for uses on canopies covering fighter planes and then made its way into space on astronaut visors and space shuttle windshields. Today it is readily available to the public. It impact resistance makes the material extremely suitable for sports, industrial safety goggles, and children's eyewear.
Scratching: The reason for polycarbonate lenses' impact resistance is because of its "softness". Softer materials will flex instead of fragment when met with great force. However, the property allows lenses to be scratched easily. Therefore, every single one of our polycarbonate lenses is multi-coated with hard coating that forms a protective layer around the lenses allowing the lenses to be free from scratches while retaining its impact resistant qualities.
UV Protection: Polycarbonate lenses inherently carries UV protection properties that blocks nearly 100% of the UV rays from entering the back of the retina.
Scratching: The reason for polycarbonate lenses' impact resistance is because of its "softness". Softer materials will flex instead of fragment when met with great force. However, the property allows lenses to be scratched easily. Therefore, every single one of our polycarbonate lenses is multi-coated with hard coating that forms a protective layer around the lenses allowing the lenses to be free from scratches while retaining its impact resistant qualities.
UV Protection: Polycarbonate lenses inherently carries UV protection properties that blocks nearly 100% of the UV rays from entering the back of the retina.
Aspherical lens design reduces lens thickness and weight. Furthermore, it eliminates spherical aberration and barrel distortion resulting from traditional lens design. The image will be sharper and clearer.
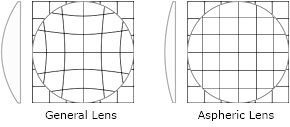
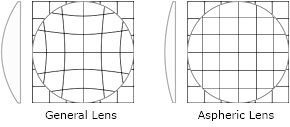
Lenses have a specific gravity of 1.20 g/cm3. Not only is the material lighter, because of a higher index refraction of 1.60, less materials needed to be used to make the prescription.
All of lenses have excellent impact resistance to protect the wearer from injuries. The lenses have passed both the European Committee for Standardization (CEN) Strength Norm Test and the US Food and Drugs Administration (FDA) Balldrop Test.
The impact resistance of Polycarbonate monomer gives plastic lenses the strength to sustain stable curve design.
FDA Ball Drop Test Parameters:
1. The impact test will consist of a 5/8 inch steel ball weighing approximately 0.56 ounces
2. The ball should be dropped from a height of 50 inches from the horizontal upper surface of the lens
3. The geometric center of the lens should be struck by the ball within a 5/8 inch diameter circle
4. There cannot be anything restricting the fall of the ball
5. A tube may be used to guide the ball to the lens; the ball may be dropped through a tube extending to within approximately 4 inches of the lens.

1. The impact test will consist of a 5/8 inch steel ball weighing approximately 0.56 ounces
2. The ball should be dropped from a height of 50 inches from the horizontal upper surface of the lens
3. The geometric center of the lens should be struck by the ball within a 5/8 inch diameter circle
4. There cannot be anything restricting the fall of the ball
5. A tube may be used to guide the ball to the lens; the ball may be dropped through a tube extending to within approximately 4 inches of the lens.
